複雑な工程の製造スタイルに合うスケジューラを
計画立案時間、リードタイムとも大幅に短縮
浜松ホトニクス株式会社様 電子機器
- 2005年6月 作成
- 表示用PDFダウンロード
- 印刷用PDFダウンロード
「どうすればスケジューリングの時間を短縮することができるのか」──。
浜松ホトニクス株式会社システム事業部システム製造部は、長い間、その問題に直面していました。 毎年のように試行錯誤を繰り返しますが、思うような成果が出ません。そして2年前、「何か手を打たないとこの状態は改善されない」と、ついにFLEXSCHEの導入を決めます。
「まだ完全に使いこなせている段階ではないのですが、すでに効果が出ています」と、第1製造グループの町田卓也氏。FLEXSCHEの導入によって、製造現場はどう変わったのでしょうか。町田卓也氏と、同じく第1製造グループの山田素史氏にお伺いしました。
複雑な工程や多品種少量化で、長くなるスケジューリング時間
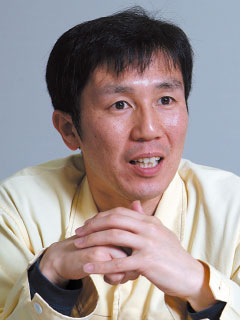
システム事業部システム製造部
第1製造グループ
町田 卓也 氏
浜松ホトニクス株式会社の創業は1953年と、すでに半世紀以上もの歴史を誇ります。主に製造しているのは光電子増倍管、イメージ機器および光源、光半導体素子、画像処理・計測装置などで、ノーベル物理学賞を受賞した小柴昌俊・平成基礎科学財団理事長の「スーパーカミオカンデ」に使われた20インチの光電子増倍管も、浜松ホトニクスでつくられたものです。
今回FLEXSCHEを導入したのはシステム事業部システム製造部第1製造グループ。浜松市内にある都田製作所と常光製作所内にあり、所属の従業員数は約50名。ここでは主に大学や各種研究機関向けの検出用各種デジタルカメラなどの画像処理・計測装置が製造されています。
デジタルカメラの工程は大きく3つに分かれます。1つは「基板工程」。主にマウンターで製造し、この作業は常光製作所でおこなっています。2つめが「線材工程」。カメラとコントローラーをつなぐ配線のことで、外注によって対応しています。3つめが「組立・調整」。出来上がった基板、線材などを組立・入庫検査する作業で、都田製作所が担当しています。
「大まかな工程で言うとこの3工程ですが、細かい工程を入れると40にもなり、他業種と比べて工程が非常に複雑です。さらに、組立や調整はすべて手作業でおこなうため、単純に流れ作業というわけにはいきません。そのため、どうしても計画立案に時間がかかってしまうのです」
複雑な工程、手作業という問題に拍車をかけたのが、「多品種少量生産」という時代の流れでした。小ロット化が進み、クライアントの要望に応えるために、高感度カメラ、近赤外用カメラ、紫外用カメラなど、その種類も大幅に増えました。
「その昔は計画立案はすべて手書きでしたが、それではさすがに時間がかかりすぎるため、マイクロソフトのスケジュール管理ソフトMicrosoft Projectを使い始めました。しかし、ビジュアル的にわかりやすくなったものの、自動スケジューリングではないので結局は人がスケジュールを立てなくてはならず、特にスケジューリングの面で思ったような効果は出ませんでした」
第1製造グループの計画立案は、まず大日程計画を町田氏が組み、基板工程は常光製作所の担当者・宮崎氏、外注の工程は山田氏、そして組立・調整を町田氏が組んでいましたが、膨大な時間がかかり、特に常光製作所では1週間の計画立案に10時間もかかりました。
そして、もう1つ大きな問題がありました。在庫の問題でした。在庫を減らすために、受注が見込めるものは見込生産、そうでないものは受注生産で対応していましたが、それでも在庫を抱えてしまいます。そこで「在庫を減らすにはやはりリードタイムを短縮して回転率を上げるしかない」という結論に至りました。
スケジューリング時間とリードタイムの短縮。この2つの課題を克服するために、ついにスケジューラ導入を決め、改革に着手することになります。2003年春のことでした。
柔軟性の高さが、FLEXSCHE導入の決め手に
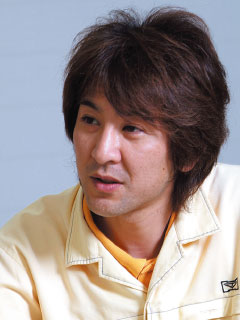
システム事業部システム製造部
第1製造グループ
山田 素史 氏
プロジェクトチームは町田氏、山田氏と、常光製作所の宮崎氏。3人が悩んだのは「どのスケジューラを導入すべきか」ということでした。
「もっとも重視したのは、我々の製造スタイルに対応できるスケジューラかどうかということでした。デジタルカメラや計測器の工程はとても複雑で、なおかつ作業も機械ではなく手作業が中心となります。さらに材料の変更なども多く、そうした特殊な条件の製造スタイルにも対応できるスケジューラでないと導入する意味がないだろうと考えていました」
インターネットや展示会で情報収集。そのなかで4、5社のスケジューラが候補として残りました。素人でもわかりやすいMicrosoft ExcelのCSVデータが扱え、まとめ計画、作業分割、さらに従業員の休みなどの作業制約が設定できるといった標準機能などから、最終的に2つのスケジューラに絞りました。
「もう1つのスケジューラは標準機能はたくさんあったのですが、うちが本当に欲しいと思っていた機能がことごとくなかったのです。実は、そのスケジューラは他の事業部で使っており、担当者の話を聞いてみると『工程の少ない設備産業には向いているけど複雑な工程には合わない』とのこと。実際にメーカーに『こんな機能はできませんか』と訊いても、『難しい』といわれてしまう。でもFLEXSCHEは『それもできる』と。柔軟性が非常に高いんですね。価格的にも予算内に収まりそうだったため、最終的にFLEXSCHEに決まりました」
FLEXSCHEの導入は、機能や仕様に関してはプロジェクトチームの3人が担当し、マスターデータ登録については女子社員が担当することで進められました。その際、導入に当たって大きな力となったのがインテグレーターの存在でした。
「初めてのことなので何から手をつけていいのかわからなかったのですが、インテグレーターが導入の道筋を示してくれたことで、その後の作業がスムーズになりました」
そのインテグレーターの力を借りてプロジェクトチームがおこなったのが、標準機能の利用方法の検討とカスタマイズしなければならないものの見極めでした。
「要望は非常に細かい部分にまで及んだため、すべてカスタマイズでないと対応できないのではないかと思いましたが、問い合わせてみると標準機能で使えるものが数多くあることがわかり、フレクシェさんのサポートによって使えるようになりました。それでも足りない部分のみを有償サポートで補うことで、要望した機能のほとんどを取り入れることができました」
中でも「とても助かった」と語るのが『正式名称検索機能』でした。
「オーダーの名称に、仮オーダー名と正式名称の2つがあったのですが、我々は仮オーダーの存在しか知らなくて、正式名称のオーダーを引っ張り出すのに困っていたのです。それが簡単に検索できるようになった。この便利さは特に深く印象に残っています」
FLEXSCHE導入に当たってプロジェクトチームが気をつけたことは、「現場に混乱を招かない」ことでした。それまで作業日程計画書はMicrosoft Projectを使っていたため、いきなりFLEXSCHEのデータを見せると現場が混乱すると判断。そこで、FLEXSCHEから必要なCSVデータを取り出し、それをMicrosoft Projectにインポートすることで、見た目として、以前と変わらない作業日程計画書を渡すことができました。
そして2005年3月にFLEXSCHEを試験的に稼動、4月から本格稼動しています。
導入後直ちに、リードタイムが10稼働日から8稼働日に短縮
FLEXSCHEに登録したマスターデータはほぼすべての製品に渡り、資源の登録も常光製作所のマウンターはもちろん、所属の全ての作業者、外注先にまで及んでいます。社員1人1人の能力値や休日などの作業制約の設定もおこない、多重資源の管理も実施。この結果大きく変わったことがあります。計画立案者が1人になったことです。
「以前は、町田が大日程計画を立て、その後の基板、外注、組立・調整の細かい日程を3人で分担して組んでいましたが、FLEXSCHEは大日程を組むとそれがそのまま中日程、小日程と実現可能な細かいスケジュールに反映されるため、あとはチェックするだけで済むようになりました」
FLEXSCHEが、特に大きな成果を発揮しているのが常光製作所です。計画立案時間が、かつての10時間/週から6時間/週と大幅に短縮され、空いた時間を使って次の改善テーマに取り組むことができるようになったのです。
「常光製作所には当社で『業務依頼』と呼ぶデータのない依頼があり、それを入れ込むための調整がどうしても必要なのですが、それ以外は全てFLEXSCHEで対応できるので、期待通りの効果が出ました。作業指示も『何時から何時まで』と細かい指示へと変わりましたが、実現可能なスケジュールになっているため、現場からの不平も今のところ出ていません」
また、課題だったリードタイムの短縮も図ることができ、組立から入庫まで10稼働日だったリードタイムは、現在では8稼動日となっています。「なぜ短縮につながったのか、正直はかりかねているところもあります。ただ少なくともいえるのは、FLEXSCHEを導入した途端にリードタイムが短くなったことです。以前のスケジュールはある程度余裕をもたせて組んでいたところがありましたが、時間単位で細かくスケジュールを組めるようになったことで、『余白』の部分が圧縮され、短縮に結びついたといえると思います。まだ導入して日が浅いため在庫削減まではいっていませんが、このままリードタイムの短縮が続けば、はっきりとした効果が出てくるはずです」
課題を克服して、さらなる改善を目指す
FLEXSCHEを導入してまだ数ヶ月ですが、さらなるステップアップに向け、「今後は1つ1つの課題をクリアしていきたい」と語ります。「常光製作所はうまくいきましたが、都田製作所の計画立案に費やす時間はまだまだ改善の余地があります。原因の1つが当社の社内ルールです。他事業部で加工してもらう際、何曜日までに材料を渡さないと製造できないといった細かいルールがあるため、その場合どう入れ込むかといった他事業部との交渉がどうしても必要になります。また、特殊な材料などは仕入日が決まっており、それもどう調整して納期に間に合わせるのかということを考えなければいけません。こうした問題を少しずつクリアすることで、FLEXSCHE導入の効果をさらに高めていきたいと思っています」
また、外注時のMRPデータの取り扱いも大きな課題の1つでした。外注にはMRPデータで渡していますが、FLEXSCHEのデータと微妙に違うため、山田氏がインターフェース役となり、違いを見つけてMRPに置き換えるという作業がありました。「ただ、全体としてはとても満足しています。中でも助かったのは導入後のフォロー体制です。スケジューラを使うのは初めての経験なので、どうしてもわからないことで出てきます。現場にとっては逼迫した問題で、そのときはインテグレーターが迅速に対応してくれ、非常に助かりました。メールや電話のやりとりで、的確に指示してもらえたためすぐに解決できました」
FLEXSCHEの導入効果と迅速なインテグレーターの対応を目の当たりにし、現在浜松ホトニクスでは、電子管事業部でFLEXSCHEの導入を前向きに検討しており、同じシステム事業部システム製造部の第2製造グループでも導入を考えているとのことです。
「当面の目標は、現在1人でおこなっているスケジューリングを複数の社員が扱えるようにすることと、使っていない機能の習得です。FLEXSCHEはすでに我々の日常業務に溶け込んでいます。ぜひこれを最大限に活用して、さらなる改善に取り組んでいきたいと思っています」
インテグレーターの声
FLEXSCHEは柔軟性が高いため、導入にもさまざまなケースがありますが、今回の場合、カスタマイズの要求が多岐にわたったのが特徴的でした。検討時からのお付き合いだったため、フレクシェから直接では、逆に話が通じないこともあると考え、私がインターフェースの役を務め、曰く言いがたい部分をうまく翻訳してフレクシェに伝えることで、お客様がほしい機能が的確に入るように努力しました。
導入後も問い合わせが何度もありましたが、物理的な距離の問題を少なくするために、画像を送ってもらい、互いに同じ画面を見ることで問題解決に当たりました。お蔭様で満足していただいているようですので、とてもうれしく思います。今後もご質問には迅速に答え、可能な限りサポートしていきたいと思っています。
お客様情報
浜松ホトニクス株式会社様
本社 | 静岡県浜松市砂山町325-6日本生命浜松駅前ビル |
---|---|
都田製作所 | 静岡県浜松市新都田1-8-3 |
常光製作所 | 静岡県浜松市常光町812 |
URL | |
設立 | 昭和28年 |
事業内容 | 光電子増倍管、撮像管、光源、光半導体、画像処理・計測装置等の製造。 |
売上高 | 704億6600万円(平成16年9月期)連結 |
上場 | 東証一部 |
従業員数 | 2,249名(パートタイマー、海外出向者等を除く) |
特徴 | 光電子増倍管で世界シェア6割を誇る。「スーパーカミオカンデ」の光電子増倍管は有名。 |