量産品生産の要、タイ工場にFLEXSCHEを導入
SAPとの連携で、後補充生産におけるラインの平準化を実現、
生産効率も向上
株式会社キッツ様 産業機械
- 2014年7月制作
- 表示用PDFダウンロード
- 印刷用PDFダウンロード
日本を代表するバルブの総合メーカー、株式会社キッツ(以下、キッツ)。国内はもとより世界で高い評価を得ている同社は、2010年に策定した長期経営計画「KITZ Global Vision 2020」において地域統括会社の設立など現地密着体制を構築し「バルブ事業の世界トップ3を目指す」という目標を掲げています。
「KITZ Global Vision 2020」の中で重要な柱の1つが、グローバル経営基盤の強化を目的とする海外拠点へのSAP導入です。キッツグループの標準的な業務やシステムを考える上でモデルとなるタイ工場への導入が2012年にスタート。同工場が抱えていた「後補充生産における平準化」と「的確かつ迅速な納期回答」の2つの課題に対しFLEXSCHEを採用することで解決を目指しました。
生産計画はもとより納期回答の要件にも対応可能なFLEXSCHEとSAPを導入し、2013年、FLEXSCHEによる新生産計画システムの本稼働に成功。納期回答業務の標準化を実現するとともに、実行計画の結果が指示として現場と連動したことでラインが平準化され、生産効率の向上や部品欠品の解消などによる工数削減につながっています。今回の成功ノウハウのもと、他拠点に対してもSAPとFLEXSCHEの導入・展開を検討しています。
グローバル経営基盤の強化を目的に海外拠点にSAPを導入
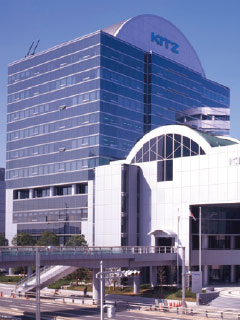
株式会社キッツ
水道、石油、ガスなどライフラインの安定供給に欠かせない部品の1つがバルブです。バルブは流体を制御するという機能から、住宅、オフィスビル、石油・ガスプラントなど利用シーンが多岐にわたっています。
日本を代表する総合バルブメーカーのキッツは、青銅、黄銅やステンレス鋼、鋳鉄、鋳鋼など様々な材質や形状、口径の異なる9万種以上の商品ラインアップを有し、お客様企業からの要求にタイムリーに応えています。また鋳造から加工、組み立て、検査、出荷まで全ての工程を社内で行う一貫生産体制は同社の強みとなり、企業理念「キッツは、創造的かつ質の高い商品・サービスで企業価値の持続的な向上を目指します」を実現する基盤となっています。
国内はもとより、世界でも「流体コントロールのKITZ」と称されるほど評価の高い同社は、グローバルでさらなる成長を果たすべく長期経営計画「KITZ GlobalVision 2020」に取り組んでいます。3極(欧州、米州、アセアン)2拠点(中国、インド)を世界の重点エリアと位置づけ、販売、マーケティング、技術、ストックなどの複合機能を備える地域統括会社を設置し、地域密着型体制のもと「バルブ事業における世界トップ3」を目指しています。
経営とITの一体化が進む現在、グローバル経営においてもITの活用は不可欠です。同社は「KITZ Global Vision 2020」の一環として経営基盤の強化を目的に海外拠点へのSAP導入を実施しています。
「SAPの導入を開始したのは2009年の中国工場が最初でした。2012年には量産製品の主力工場であるタイ工場に導入し2013年に本稼働しています。タイ工場はキッツグループの標準的な業務やシステムを考える上でモデルとなるべき工場です。タイ工場の販売/生産状況、販売/生産実績、原価実績、会計情報などの見える化を図り、キッツグループにおけるグローバル共通の基準づくりを推進することも重要な目的でした」と、情報システム部長 小澤敏氏は話します。
後補充生産における平準化の実現は急務の課題
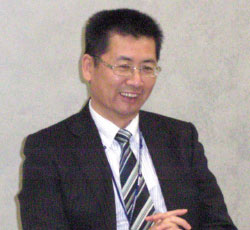
IT統括センター 情報システム部長
小澤 敏 氏
タイ工場において課題となっていたのが、必要最低限の在庫を持ち使用した分だけ補充する後補充生産に伴う「供給と補充のタイミングの乖離」でした。この課題を解決するためには、各生産ラインで1日にピッキングされる数の平準化を図り、ラインが過負荷、負荷不足にならないように計画を立てることが必要です。
「最終工程である製品の組み立ての平準化を実現することで、前工程の部品も平準化できるようになり、部品加工から素材に至るまで安定した生産が可能となります。製品の平準化計画をどのように実現するかが重要なテーマとなりました」と、生産企画グループ 米倉健太氏は振り返ります。また、ほとんどの製造ラインが後補充生産品と受注生産品を製造(混合ライン)しているため、混合ラインにおける平準化もポイントとなりました。
平準化計画の実現に必要な計画システムは自社開発しましたが、従来の計画システムには多くの課題がありました。「従来の計画システムは生産の実態と乖離している点が多かったため、人手による調整に手間と時間を要し、お客様に対して迅速な納期回答を行うことが困難でした。
また計画システムと言っても負荷の山積みシミュレーションを行っているだけで、その結果を生産の指示につなげていなかったため、計画担当者の頭の中にある計画をもとに生産活動が行われているというのが現状でした。計画に関するノウハウは人に依存しており、ノウハウが継承されないという課題も抱えていました」と米倉氏は話します。さらにタイ工場では平準化による生産効率の向上と迅速な納期回答の実現が急務の課題となっていました。そこで同社はSAPとともに計画システムを導入することを決断。計画システムの選定において次の3つのポイントが重視されました。
1. 納期回答
お客様からの納期問い合わせに対し、工場の能力に裏付けられた納期回答を実現する。また、納期回答済み/未受注案件の予約情報と実際の受注を関連づけて負荷管理することで回答した納期どおりに確実に生産を行う。
2. 実行計画
受注生産を行う品目の受注に基づき、確実な部品供給と効率的な段取りを行える生産を実行する。また実行計画で立案した受注生産計画を生産指示として生産現場に伝達する。
3. ピッキング計画
後補充生産を行う品目の受注に基づき、製品組み立てや組み立て工程に供給する部品生産を品目の偏りなく平準化するために完成品ストアから引き取りを実施する。またピッキング計画で立案した引き取り計画を出荷ピッキング指示として生産現場と倉庫に伝達する。
上記3つのポイントのうち実行計画とピッキング計画は計画システムを刷新することで実現できると想像していましたが、「納期回答」を実現するためにどのようなシステムを構築すれば実現できるのか、日々検討を重ねていました。「計画システムについては複数の会社より提案を受けました。しかし納期回答に関する当社の要件、要求については各提案会社から『できない』という回答ばかりでした。唯一FLEXSCHEの提案だけが『できる』との回答でしたので正直なところ驚きました。『できる』と回答したFLEXSCHEについていろいろと調査したところ、後補充生産に伴う当社の特殊な業務要件に応える優れた柔軟性があることに気がつきました。
またカスタマイズすることができる点についてもFLEXSCHEを高く評価するようになりました。FLEXSCHEの導入支援を行う宇部情報システムさんから適切なご提案をいただいたことも採用を後押ししました」と米倉氏はFLEXSCHE採用の理由について話します。小澤氏は計画システムを自社開発した経験に基づき、FLEXSCHEの使いやすさについてこう話します。「直感的な操作は私たちも自社開発で非常に苦労して実現した覚えがありますが、作業を任意の日時や資源にドラッグしてスムーズに手修正できるガントチャートなどFLEXSCHEの操作性の完成度の高さには大変驚かされました。」
平準化を実現するために「負荷計画」と「実行計画」の2つに分けて立案
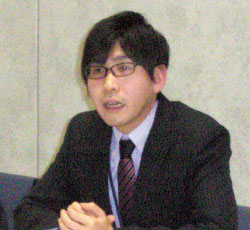
生産企画グループ
米倉 健太 氏
今回、重要なテーマである平準化計画の立案では「ライン能力の最大限の活用」と「制約を加味した実行可能な計画」の2点が大きな課題でした。この2つの課題をクリアするために引き合いの段階で納期回答の仕組みを実現する「負荷計画」と、受注が入ってから生産計画を立てていく「実行計画」を分けて考えることにしました。「後補充生産と受注生産の比率や1日の生産量、リードタイムなどの制約条件を加味し、ラインが過負荷、負荷不足にならないように負荷計画を立案し、お客様からの納期問い合わせに対し納期回答を行います。また受注が確定した後、実行計画を立案しその結果を出荷ピッキングや製造指示につなげていきます」と、システム開発グループ 井出征峰氏は話します。
新生産計画システムではSAPから納期問い合わせのデータがFLEXSCHEにデータ連携され、FLEXSCHEで自動スケジューリングを行い、その結果をSAPに返します。そしてお客様が納期回答を確認し確定オーダーを入れると、SAPから受注入力のデータがFLEXSCHEにデータ連携され、FLEXSCHEで自動スケジューリングを行い担当者の微調整後、SAP側に生産指示を出します。(参考:新生産計画システムの概要)
新生産計画システムのメンテナンスは本社側で行いたいためFLEXSCHEのサーバは日本本社に設置し、タイ工場の担当者はターミナルサービスを利用してFLEXSCHEを操作する形をとっています。タイ工場でFLEXSCHEを使って計画を立案するのはタイ人のスタッフです。英語のマニュアルを利用し、重要なところだけタイ語に翻訳して運用しています。「タイ人のスタッフには『納期回答でもデータの裏付けが必要である』という点についてじっくり時間をかけて説明しました。意識改革が伴うため、理解してもらうまでには長い時間がかかりました」(井出氏)。
新生産計画システム稼働後、数か月で生産効率が向上
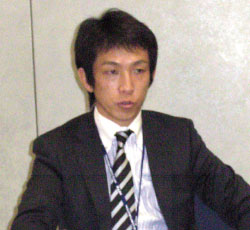
IT統括センター 情報システム部
システム開発グループ
井出 征峰 氏
2013年、タイ工場においてFLEXSCHEによる新生産計画システムの本稼働後、導入効果が顕著に表れてきました。「まず納期回答業務の標準化です。従来、納期回答は負荷積みの結果を見た上で計画担当者が豊富な製品ラインアップや製品を構成する様々な部品、他のオーダーなどの制約条件を頭の中で考えながら回答していました。現在はFLEXSCHEにより各種制約を考慮した生産完了日が算出されることから、属人的なノウハウは不要となり的確かつ迅速な納期回答を実現しています。納期回答に関してキャンセル期間を定めるなどお客様との間でルールを決めて運用することで、これまで人手に頼っていたスケジューリングもシステム化でき、業務の大幅な効率化が図れました」(井出氏)。
また平準化により生産効率も向上しました。「新生産計画システムがスタートして3カ月後には、タイ工場から生産量が増加したという報告がありました。実行計画の段階でラインの平準化を実現し、実行計画から指示を出し、その指示に基づいて生産することができたことによる効果です。部品欠品などの異常対応の工数も削減されています」(米倉氏)。さらに計画業務の工数も削減できました。導入以前は4人の生産計画担当者が計画を立案していましたが、導入後、1人の担当者が30ライン以上の計画立案と納期回答を行っています。
今後の展開について「現在、納期回答は日に2回の計画ごとに回答する形をとっていますが、営業部門から問い合わせがあった場合、すぐに画面に回答が表示されるなどリアルタイム連携を図っていきたいと考えています。特殊仕様品を含む計画業務の再構築も今後の課題です。また他拠点へのSAP導入においてタイ工場での成功ノウハウをもとにFLEXSCHEも合わせた展開を検討しています」と小澤氏は話します。流体制御のプロフェッショナルとして世界を舞台に活躍するキッツグループ。同グループのグローバル経営を生産計画の面から支えるFLEXSCHEの役割は同社の成長とともに一層大きくなっていきます。
インテグレーターの声
今回のプロジェクトは納期が非常にタイトだったため、一次開発の終了後、キッツ様にテストなどの検証を行っていただき、その間に二次開発を進めるなど3つのフェーズに分けて作業を進めました。納期を遵守できたのも、キッツ様のご協力があればこそと感謝しております。
超短期でのシステム稼動を実現するために、カスタマイズは極力行わない方針のもと、FLEXSCHEの豊富な機能を活用することにより、お客様のご要望の大半が実現できました。納期回答の機能に関してはご要望に応えるべくいろいろと検討を重ね、様々な提案を行い、お客様とともに構想を練りました。今回は、キッツ様にいろいろとご教示を賜りながら互いに協力しあうことで、ご要望を満たす新生産計画システムを実現できたと考えています。
今後も今回築いた信頼関係を大切に、キッツ様のさらなる発展に貢献できるよう力を尽くしてまいります。
導入企業概要
株式会社キッツ
設立 | 1951(昭和26)年1月26日 |
---|---|
資本金 | 21,207,084,670円 |
売上高 | 連結:117,355百万円 単体:64,438百万円(2014年3月期) |
事業内容 | 流体制御機器(バルブ・システム機器等)の製造・販売 |
URL | http://www.kitz.co.jp/ |