FLEXSCHE導入により作業負荷の平準化を実現
リードタイムを約40日短縮、早期納入材の量を6分の1に削減
川崎重工業株式会社様 車両
- 2012年4月制作
- 表示用PDFダウンロード
- 印刷用PDFダウンロード
陸・海・空、そして宇宙から深海まで、世界中で事業を展開する世界屈指の総合エンジニアリングメーカー、川崎重工業株式会社(以下、川崎重工)。同社はまた日本における鉄道車両製造のトップメーカーとして、新幹線をはじめ在来線、特急電車、地下鉄電車、機関車、モノレールなどさまざまな車両を国内はもとより世界に向けて送り出しています。
豊富な実績と高度な技術力を有する鉄道車両事業ですが、近年、競争が激しさを増す中、生産の効率化とコスト削減は重要な課題です。同社の車両カンパニー生産本部工作部台車課では、ダイヤ改正などによって受注が重なった場合に先行製作で対応しています。しかし実際には、製作に着手すべきタイミングの見極めが難しく、必要以上に製造リードタイムが伸びて資材の手配も早まる傾向がありました。作業負荷を平準化しつつ適切な計画立案をするべく、生産スケジューラFLEXSCHEを導入。
ボトルネック工程を中心にした作業計画により製造リードタイムを約40日短縮、資材の在庫量も6分の1に削減できました。新たに構築しつつある生産システムにもFLEXSCHEを連携させることで、モーターなどの購買品も適切なタイミングで受け入れるよう、改善を進めています。
1世紀以上の歴史を有する鉄道車両事業
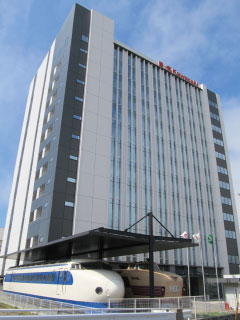
川崎重工業株式会社
兵庫工場 車両本館
1896年(明治29年)に造船事業からスタートした日本を代表する総合エンジニアリング企業、川崎重工。現在、グループミッション「世界の人々の豊かな生活と地球環境の未来に貢献する”Global Kawasaki”」のもと、造船をはじめ鉄道車両、航空機、モーターサイクルからエネルギー環境プラント、産業用ロボットまで多岐に渡る事業領域で、日本はもとより世界各国の発展に貢献しています。
同社の製品の中でも造船事業とともに1世紀以上の歴史を有するのが1906年(明治39年)から開始した鉄道車両事業です。国産化第1号蒸気機関車や日本初のアルミ車両をはじめ、鉄道史に残る名車両を数多く製造し、日本における車両製造のトップメーカーとしてのポジションを不動のものとしています。
また、新幹線車両の開発・設計への参画から、特急電車、地下鉄電車、貨車、機関車、モノレール、新都市交通まで、同社の車両製造は鉄道輸送発展の歩みそのものです。現在、マザーファクトリーである兵庫工場(神戸市)に加え、米国にも2つの本格的な工場を有し、イギリス、中国、東南アジア、中南米諸国など世界各国で事業を展開しています。
躍進を続ける同社の鉄道車両事業ですが、競争が激しさを増す中、勝ち抜いていくのは容易なことではありません。同社の強みは、豊富な実績で培った高度な技術力や開発力です。また、鉄道車両の基本構成である、車体と台車を総合的に納入できるという点も強みです。台車は、車輪と車軸を組み立てた輪軸を保持し、車体の重量を車軸に伝えるとともに走行・制御機能を備えた機構であり、鉄道車両の安全性や快適性を支えています。同社の台車にも、長年培ったノウハウや技術が活かされています。
先行製作のため材料の早期納入による在庫過多が課題に
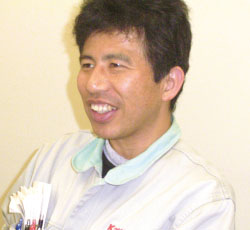
車両カンパニー 生産本部
工作部 台車課 課長
(現在 生産本部 生産技術部 基幹職)
西原 昭彦 氏
競争力の観点では、コスト削減と生産の効率化が重要な課題です。同社の台車製造においても材料費の削減とともに生産の効率化に取り組んでいますが、台車の製造はオーダーメイドに近く、多品種少量生産であることが効率性向上を阻む大きな要因となっています。
「台車は、在来線、新幹線、機関車、ゴムタイヤを使用する新都市交通の車両と、大きく4つのタイプに分類できます。例えば、新幹線と在来線では必要なブレーキ力も違ってきますから、台車の部品も異なります。また、海外の規格によっても変わってきますし、同じ在来線であってもお客様のメンテナンス作業の方法などによって少しずつ仕様や要求が違ってきます。生産計画を行う際、難しいのは多品種少量に加え、受注生産であるため見込み生産ができないことです」と、西原昭彦氏は語ります。
見込み生産ができないため、ダイヤ改正時期など受注が重なる際には先行製作で対応しています。「台車の製造において、車軸などはリードタイムが長いため1年前には受注されます。納期を厳守しないとダイヤにも影響を及ぼしてしまいますから、受注が重なった場合は先行製作に入るようにしています」と山元博司氏は語ります。
同社の台車製造は、鉄板の購買から台車の完成まですべてを社内で管理しており、約4カ月を要しています。その内容は、鉄板を削ったり曲げたりする作業で3週間、溶接などで1.5カ月、部品の取り付けや機械加工で2週間、組立に2週間。通常、新幹線、在来線などによって作業負荷が異なるため4、5種くらいの車両を混流生産しています。
「リードタイムが長く、先行製作を行うため、どうしても早めに材料を発注してしまい、在庫過多になりがちです。材料は大きなものですから場所にも制約があります。在庫過多を防止するためにリードタイムを短縮し、早期納入材の量を減らすことが必要でした」(西原氏)。
リスケジューリングと柔軟性がFLEXSCHE採用のポイント
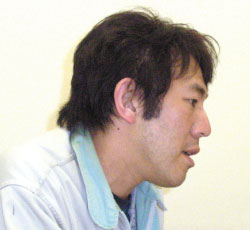
車両カンパニー 生産本部
工作部 台車課 基幹職
(現在 プロジェクト本部
アジアプロジェクト部
基幹職)
山元 博司 氏
リードタイム短縮は生産計画を立案する時点で考慮しておかなければ、実現できません。従来、現場の班長などが勘と経験に基づいて、表計算ソフトなどを駆使して生産計画を立てていましたが、早めに材料を仕入れて在庫をもって仕事をするという習慣ができていました。
「1台の台車の部品点数は約350種、最終工程の組立てを除き1台車で約1,000工程、作業スタッフは約300人と、これだけ複雑かつ膨大な作業のスケジューリングを正確に行うというのは人間の管理能力を超えています。そこで、スケジューラの導入検討を始めました」(西原氏)。
複数のスケジューラの検討を重ねた末、採用されたのがFLEXSCHEでした。その理由について山元氏は次のように語ります。「台車課の場合、多品種少量生産のため、実際の製造現場では色々なことが起こり、状況が刻々と変化します。例えば、急遽、休んでしまったスタッフへの対応や、完了しなかった作業を翌日の作業として再度スケジューリングを行うなど、当社の実情に柔軟な対応ができるか、という点を重視しました。また当社の場合には作業データ量が膨大で作業変更も多いですから、素早くリスケジューリングできる点も採用の大きなポイントになりました」。
リードタイムを約40日短縮、早期納入材の在庫量も約6分の1に削減
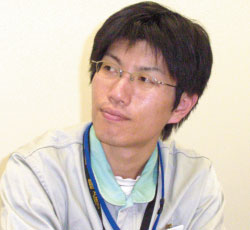
車両カンパニー 生産本部
工作部 台車課
藤井 博之 氏
2008年春頃、FLEXSCHEを導入、スケジューリングした結果をもとに作業指示を出し、実績を取り込んでスケジュールの調整を行っています。導入効果として山元氏はまず作業負荷の平準化を挙げました。「FLEXSCHEを使って、さまざまな設備の間で作業負荷を平準化しつつ、ボトルネック工程を中心とする適切な計画を自動的に立てています。1つ1つの部品ごとにボトルネックは異なります。これまではボトルネック工程を管理することが困難であったため、前工程の着手が早過ぎ、後工程では手待ちが発生していました。FLEXSCHE導入1年後で最大30万作業ありましたから、人間の手作業ではとても対応し切れるものではありませんでした。」
10分、20分で終わってしまう作業が連続すると、必然的にボトルネックを管理することは困難となります。FLEXSCHEでスケジューリングすることにより、設備がフル稼働状況であるといったことも一目瞭然になることから、いままで見えにくかったボトルネックが顕在化してくるといった効果もありました。「FLEXSCHEが最適に割り付けることで、ボトルネック工程の前工程着手が早過ぎたり、後工程での手待ちといった、1つ1つの非効率性を排除して全体として作業工程の効率化を実現しています。その結果、リードタイムを約40日短縮できました」と山元氏は話します。
リードタイムの短縮により、懸案だった早期納入材の在庫量も約6分の1に削減、スペースも100㎡以上の有効活用が図れました。数か月先の状況判断が的確に行えるようになったことで、外注先に対して入札を求めることが可能となりコスト削減も実現。また、無駄な外注がなくなり内製化率も向上しました。
FLEXSCHEで部品の製作状況を管理、情報の共有も実現
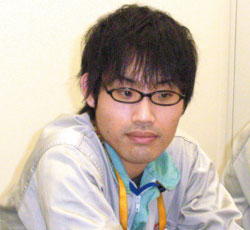
車両カンパニー 生産本部
工作部 台車課
武下 洋 氏
FLEXSCHE導入による新しいスケジューリングに基づく仕事のやり方が現場に定着するまでには1年間という時間が必要でした。「従来、現場に任せていた細かい部分までスケジューリングしていますので、導入後、毎週、現場のスタッフを集めて説明やアドバイスを行いました。また現場からの要望に対していろいろと話し合いもしました。現場との意見交換や調整作業などには多くの時間を費やしました。」と藤井博之氏は語ります。
現場の要望で多いのは、作業指示書などの帳票の見やすさ、わかりやすさです。「現場で必要とする情報をFLEXSCHEから抽出しています。作業指示書のみならず、作業が完了できなかった部分について工程会議でフォローアップするための帳票や、各工程間でやり取りする伝票、素材納入の際の納入指示書や納入管理表などさまさまざまです」と武下洋氏は語ります。進捗管理についても「ある作業だけを見ていては、その工程が間に合っているのかどうかわかりません。現在では現場の情報を吸い上げ、進捗管理情報を1つのシートでまとめて見えるようにし、状況を的確に把握できるようにしました。関係者全員がその情報を共有できることも大きなメリットですね。」と藤井氏は指摘します。
FLEXSCHEを使いこなすうちに運用が次第に改善されてきたと、武下氏は話します。
「過去に作ったマスターデータや作業実績が蓄積されるに従い、それらを利用して新規のデータを効率良く作成できるようになりました。また、少しずつスケジューリングルールを改良して、リスケジューリング時間を5分の1にまで短縮できました。今後もさまざまな工夫に努めながら、FLEXSCHEのさらなる性能向上にも期待しています。
計画を立てる側と現場と互いにわかり合った中で運用
現在、FLEXSCHEは現場に定着し、なくてはならない存在となっています。「これまでの「やらされている」といった感覚から、今では「上手く自分たちで使っていこう」というように現場の発想も変ってきました。現場の改善とセットで進めている側面もあります」(藤井氏)。
FLEXSCHE導入成功のポイントについて、「一般的に生産スケジューラの導入は、管理部門が携わることが多いと思いますが、今回は台車課が自身で導入したことが功を奏したと考えています。スケジューリングしている者が製造現場も担当しており、現場スタッフと毎日コミュニケーションをとっています。立案者と実行者の相互理解に基づいて運用しているのです。」と山元氏は説明します。
今後の展望について山元氏は「現在、FLEXSCHEのスケジューリング結果に基づく納入指示は資材関係だけですが、弊社の生産システムとFLEXSCHEの連携によりモーターなどの購入部品にも対象を広げたいと考えています。これにより購入部品を適切なタイミングで納入することが可能となります。また、いまは作業完了のデータしかとっていませんが、着手データを加えることでスケジューリングの精度の向上も図りたいですね」と語ります。
さらに、西原氏はこれからの課題についてこう述べます。「スケジューラの運用ではデータのメンテナンスが重要です。現在、特定の人しかFLEXSCHEを操作していませんが、今後はFLEXSCHEに習熟した人を増やしていきたいと考えています」。
世界の国々において交通網の中心的役割を担っている鉄道。1世紀以上に渡って積み上げた豊富な実績とノウハウを活かして時代や社会のニーズに応える川崎重工車両カンパニー。FLEXSCHEがその生産計画の一翼を担っています。
導入企業概要
川崎重工業株式会社様
設立 | 1896年(明治29年) |
---|---|
資本金 | 1,043億円 |
事業内容 | 船舶、鉄道車両、航空機、宇宙機器、ジェットエンジン、各種エネルギー設備、各種舶用機械、鉄鋼構造物、各種プラント、モーターサイクル、レジャー関連機器、各種油圧機器、産業用ロボット等の製造・販売 |
車両カンパニー | 日本における鉄道車両製造のトップメーカーとして、新幹線をはじめ電車・客車・貨車・機関車・ディーゼル機関車・新交通システムなどさまざまな車両を世界に送り出している。マザーファクトリーである兵庫工場(神戸市)に加え、米国にも2つの工場を有する。 |
URL |